Plastic injection molding machine are the backbone of the manufacturing process for countless industries, producing everything from automotive parts to consumer goods. However, like any machinery, they have a finite lifespan and may become less efficient over time. Recognizing the signs that it’s time to upgrade your plastic injection molding machine can save you time, money, and resources. In this article, we will explore the key indicators that signal an upgrade is necessary and how to make the most of your investment.
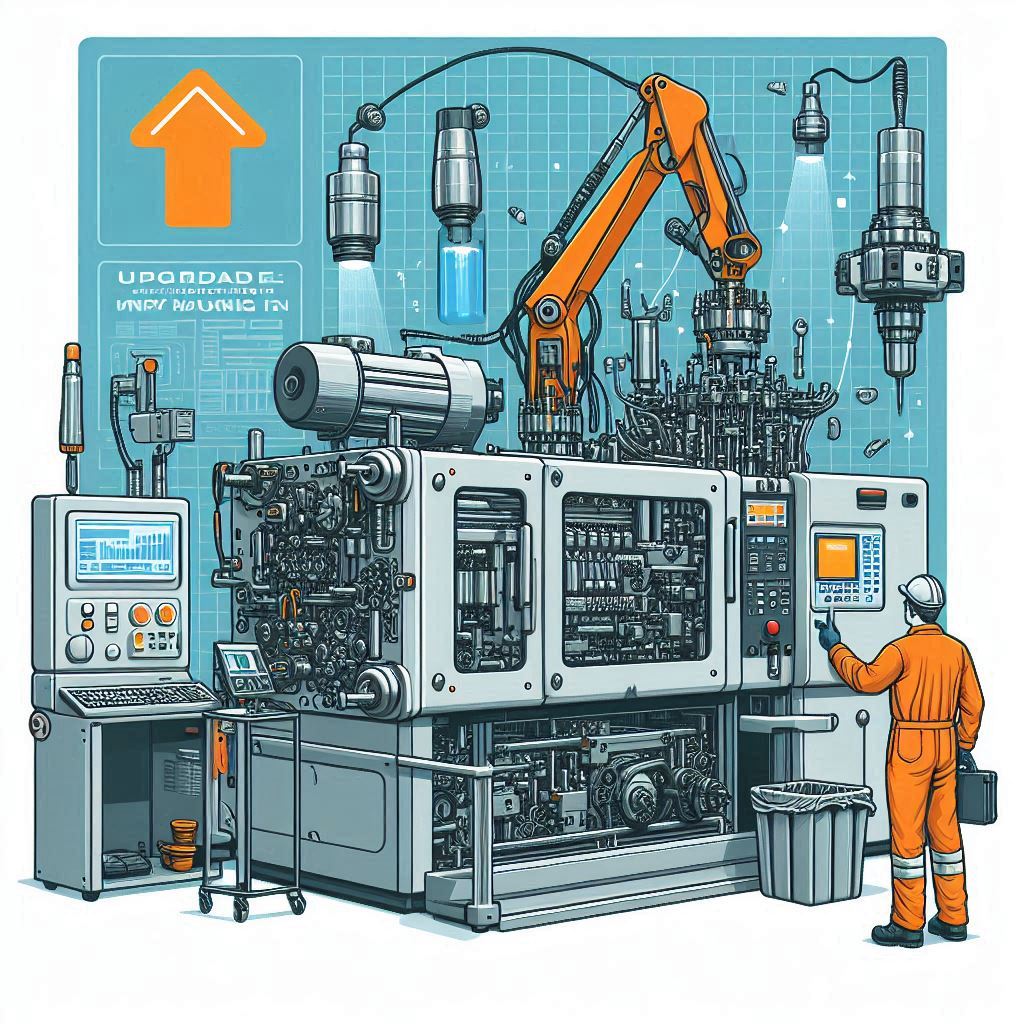
Understanding Plastic Injection Molding Machines
Before diving into the signs of needing an upgrade, it’s essential to understand the function of plastic injection molding machines. These machines work by heating plastic resin until it melts, then injecting it into a mold to create a specific shape. The process is highly efficient, allowing for mass production of complex parts with precision.
Why Upgrading Matters
Upgrading your plastic injection molding machine can lead to improved efficiency, reduced production costs, and higher-quality products. Newer machines often come equipped with advanced technology that enhances performance and reduces energy consumption. Recognizing when to make this investment is crucial for staying competitive in a rapidly evolving market.
Signs It’s Time to Upgrade Your Plastic Injection Molding Machine
1. Declining Production Efficiency
Indicator: If you notice that production speeds have decreased significantly without a corresponding increase in complexity or volume, it may be a sign that your machine is struggling.
Why It Matters: Older machines can experience wear and tear that affects their performance. This decline can lead to longer cycle times, ultimately impacting your bottom line.
Action: Assess the machine’s cycle times against industry standards. If there’s a notable discrepancy, consider an upgrade to a newer model that offers improved speed and efficiency.
2. Inconsistent Product Quality
Indicator: If you find that your products are increasingly inconsistent in quality, with variations in dimensions or surface finish, it may indicate that your machine can no longer maintain precise control over the molding process.
Why It Matters: Inconsistent quality can lead to increased scrap rates, customer complaints, and damage to your brand’s reputation.
Action: Evaluate whether your current machine is capable of producing parts within the required tolerances. Upgrading to a machine with better control features can help maintain consistent quality.
3. Frequent Breakdowns and Repairs
Indicator: An increase in downtime due to frequent machine malfunctions or breakdowns is a clear sign that your machine may be reaching the end of its useful life.
Why It Matters: Regular repairs not only increase operational costs but also disrupt production schedules, leading to lost revenue.
Action: Keep track of repair frequency and costs. If repair expenses are rising significantly, it might be more cost-effective to invest in a new machine rather than continuing to patch up the old one.
4. Rising Operating Costs
Indicator: If your energy bills and maintenance costs are steadily increasing, this could suggest that your machine is inefficient and consuming more resources than necessary.
Why It Matters: Older machines often consume more energy and require more maintenance, impacting profitability.
Action: Analyze your operating costs over time. If the trend shows a significant increase, upgrading to a more energy-efficient model can lead to substantial savings.
5. Limited Capability to Process New Materials
Indicator: If your production needs are evolving—such as the requirement to process new types of plastics or composites—and your current machine lacks the capability, it may be time for an upgrade.
Why It Matters: Newer materials can enhance product performance and sustainability, but they often require machines equipped with specific features to process them effectively.
Action: Assess whether your existing machine can handle the materials you plan to use. Investing in an upgrade that accommodates a wider range of materials can expand your production capabilities.
6. Inadequate Automation and Technology
Indicator: If your machine lacks modern automation features, such as advanced control systems or IoT capabilities, it may be falling behind in terms of technology.
Why It Matters: Automation can streamline production processes, improve accuracy, and reduce labor costs. Machines with outdated technology may not integrate well with modern manufacturing practices.
Action: Evaluate how automation and advanced technologies could improve your production processes. Upgrading to a machine that incorporates these features can enhance overall efficiency and adaptability.
7. Inability to Meet Demand
Indicator: If your current machine struggles to keep up with production demands, leading to delays and missed deadlines, it’s a clear sign that an upgrade is needed.
Why It Matters: Failing to meet demand can result in lost sales opportunities and dissatisfied customers.
Action: Analyze production capacity versus demand. If you consistently find yourself unable to meet production goals, investing in a larger or more efficient machine may be necessary to scale operations.
8. Environmental Compliance Issues
Indicator: Stricter environmental regulations and sustainability goals are becoming more prevalent in manufacturing. If your machine does not comply with these regulations, it may be time for an upgrade.
Why It Matters: Non-compliance can result in fines and damage to your company’s reputation. Newer machines are often designed with sustainability in mind, offering lower emissions and better energy efficiency.
Action: Research current environmental regulations affecting your industry. If your machine does not meet these standards, upgrading can help you stay compliant and improve your sustainability efforts.
9. Operator Safety Concerns
Indicator: If operators frequently report safety issues or if your machine lacks modern safety features, it’s crucial to consider an upgrade.
Why It Matters: Employee safety is paramount, and outdated machines may not offer adequate protection for operators, increasing the risk of accidents.
Action: Evaluate the safety features of your current machine against industry standards. Investing in a newer machine that includes advanced safety features can protect your employees and reduce liability.
10. Limited Support for Maintenance and Parts
Indicator: If it’s becoming increasingly difficult to find parts or receive support for your existing machine, it may be nearing the end of its lifecycle.
Why It Matters: Limited support can lead to longer downtimes and increased costs for repairs.
Action: Assess the availability of replacement parts and technical support for your machine. If these are dwindling, upgrading to a machine with strong manufacturer support can ensure better maintenance and service in the long run.
Conclusion
Recognizing the signs that it’s time to upgrade your plastic injection molding machine is crucial for maintaining efficiency, product quality, and competitiveness in the market. From declining production efficiency to increased operating costs and safety concerns, these indicators can significantly impact your operations.
Investing in a new machine can enhance productivity, reduce costs, and ensure compliance with industry standards, ultimately leading to higher profitability. By staying vigilant and proactive, you can make informed decisions that will benefit your business in the long run. Upgrading your plastic injection molding machine is not just an investment in equipment; it’s an investment in the future success of your manufacturing operations. read more..